From the middle of the monotonous steady hum of the equipment, the sound of the suddenly strengthened screw pumps began to be clearly distinguished.
”This draff concentration exceeded 50% dry,” says the start-up manager almost in my ear.
I open the mnemonic diagram on the tablet and find the necessary readings of the electronic densitometer: the concentration is 55%
12 months ago, an investor of one of the bioethanol plants in the Vinnytsia region called me and asked:
“What needs to be done in order not to dump the draff on the filter fields, and even better – to process the waste into a commercial product?”.
He said he sees his money pouring out with the draff every day.
There are many solutions for waste disposal, you just need to choose the most appropriate in a specific situation and the most technologically modern.
Here are some of the distillery solutions:
- Concentration of draff in an ultrafiltration unit
- Processing of draff into biogas
- Concentration of draff on a vacuum-evaporation unit
The investor and I considered each of the options.
ABOUT ULTRAFILTRATION
Installation of ultrafiltration on membrane filters will allow you to concentrate the molasses to only 20…30% dry matter (DM), and on the other side of the filter you have very salty water, which also needs to be sent somewhere. We were not satisfied with such products.
Ultrafiltration is suitable for relatively pure liquids. The installation is complex and expensive to operate. We didn’t even count how much it would cost to purchase it for our daily draff volume.
ABOUT BIOGAS
From 1 m3 of draff if you add up to 10% co-substrate (cattle manure) to it, you can get about 50 m3 of biogas. If the factory converts all the waste into biogas, it will be able to meet its energy needs.
However, at the same time, there remains the issue of disposal of digestate – dirty (about 50,000 mg O2 according to the Code of Civil Procedure) water after the methane tanks. There will be as many of them as there were draff in the beginning. For the digestate, you need to create a cascade of biological sedimentation ponds.
We calculated that a biogas factory for processing 1,200 m3 of draff per day will cost 4…5 million euros, and its construction will take 12…18 months.
ABOUT THE EVAPORATION INSTALLATION
The evaporation unit concentrates the molasses to 55…60% DM (or grain draff centrifuge for the production of DDGS to 30% of DM), while the volume of the draff is reduced by 5 times.
For example, if you have 1,200 m3 of draff per day, after evaporation there are 240 m3 of draff with a concentration of 60% and fairly clean condensate up to 1 thousand mg O2. Condensate can be returned to the technology for the preparation of mash or, after further purification, directed to the needs of the boiler house.
What is molasses draff concentrated up to 60% of DM? This is a commercial product – a full-fledged liquid fertilizer.
The main composition of draff dry substances:
Показатель | %, мас. |
---|---|
бетаин | 16…21 |
аминокислоты | 15…25 |
органические кислоты | 3…10 |
коллоиды | 13…15 |
азот общий | 6…8 |
SO42- | 0,6…4,6 |
K+ | 8,5…13 |
P2O5 | 0,1…0,2 |
Ca2+ | 0,5…2,5 |
Fe, Mn, Ni, Co, Ti, Mо и пр. | 0,12…0,14 |
Due to the high content of dry matter, concentrated bard can be stored in the same way as molasses – it does not spoil. In addition, it contains less water than native, so it is 5 times cheaper to transport.
Conclusion: we solve the problem of dumping waste on landfills – there will be no more of them, and at the same time we produce an additional product.
We set out to estimate capital and operating costs.
According to our calculations, the cost of equipment with the construction of an evaporation factory with a capacity of 40 t/h of evaporated moisture (1200 m3 bard per day) will be 1.3-1.6 million euros.
Operating expenses.
The evaporation factory is designed in such a way that it can fully heat the steam rectification plant with its own (secondary) steam. In other words, the cost of evaporation (concentration) of draff is minimal in our country – 50 kg of steam per 1 ton of evaporated moisture. When we calculated steam consumption for concentration of 1200 m3/day draff from 12% to 60% of dry matter, it turned out that the evaporation plant will consume 2 tons of steam per hour.
The conclusion is convincing – it is necessary to build an evaporation factory.
Our engineering team was given a task about designing an evaporation factory in such a way that the main equipment could be manufactured here in Ukraine. Only automation devices and pumps could be imported. And it was necessary to assemble the evaporation factory in a metal shelf so as not to burden the project with capital buildings.
According to calculations, it should be a four-sides evaporation unit with TVR thermocompression. The first two cases are falling film evaporators, and the last two are forced circulation evaporators.
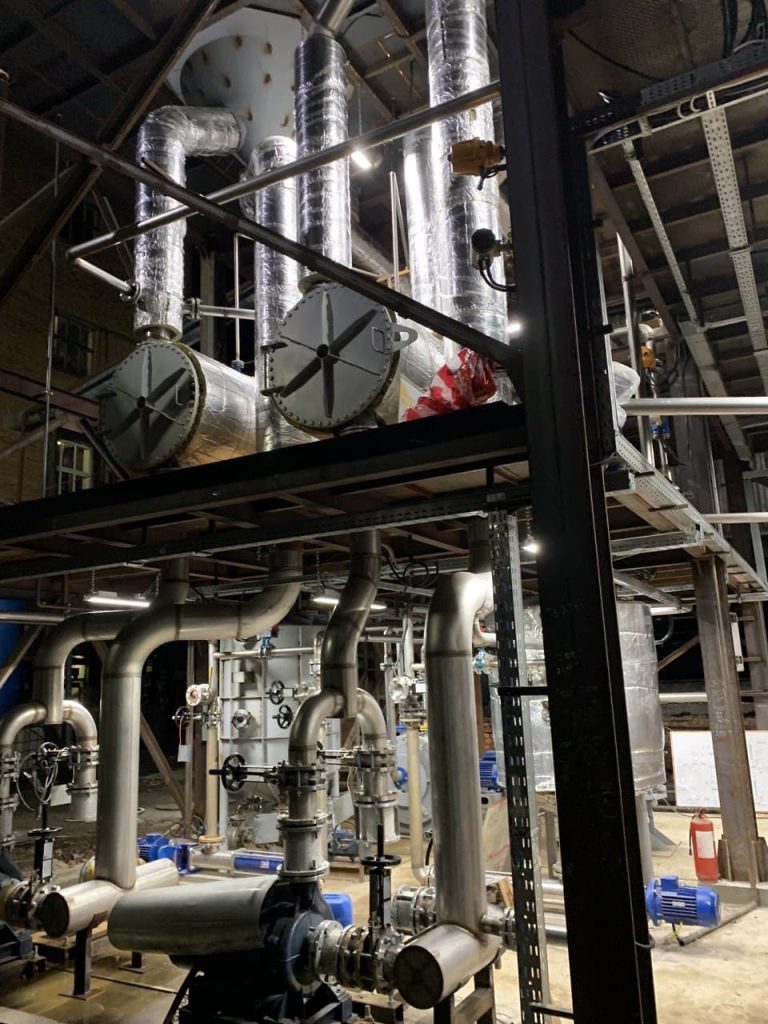
The vacuum evaporation unit contains:
2 cases — evaporating apparatuses with a falling film;
2 cases — evaporation apparatuses with forced circulation;
4 steam separators for each of the cases;
8 heat recuperators for maximum energy conservation;
1 TVR thermocompressor for heating secondary steam;
4 pump groups for draff, condensates, vacuum and product;
system of automated control of the vacuum-evaporation unit.
After two months of project work, they began to manufacture equipment and pour the foundation.
While the frame of the shelf is being erected, large-scale equipment – 13-meter casings which look like cigars of the installation – are inserted inside with the help of cranes. Then steam separators, tubular and spiral heat exchangers, condensate collectors, pump groups are placed. All this is connected with pipelines of various diameters and cables of the automation system.
Construction and installation take place simultaneously and last eight months.
At this stage, we are already planning the start of commissioning works – we are writing the regulations for the operation of the station, instructions for the operators.
A launch date has been set. Everyone is a bit worried – because this is the first evaporation station in modern Ukraine, which will process molasses and grain centrifuge
7:57 am, launch day.
The manager of the start-up of the evaporation plant determines the procedure for the actions of the personnel.
A decisive movement of his hand marks the beginning. .
The manager’s commands echo in radio stations:
- Provide water for cooling!
– Send the draff to the evaporation station!
– Start circulation pumps!
– Boiler room, we are starting to get steam!
– Control condensate levels!
6:45pm, launch day.
From the middle of the monotonous steady hum of the equipment, the sound of the screw pumps, suddenly strengthened, began to stand out clearly. .
“This draff concentration exceeded 50% dry,” says the start-up manager almost in my ear.
I open the mnemonic diagram on the tablet and find the necessary readings of the electronic densitometer: the concentration is 55%
START OF THE EVAPORATION FACTORY HAS OCCURRED
In a few weeks, we selected and installed the correct operating modes, eliminated minor installation defects, changed several pumps and valves, and brought the evaporation factory to normal operation.
The evaporation unit works: it concentrates the molasses to 60% of dry matter and heats the steam rectification unit with secondary steam.
We compare the actual production data (quantity of condensates, steam consumption for thermocompression, product concentration) with estimated ones – the difference is within the limit of error.
Therefore, we are grateful to the engineers of Agrotechnology for their accurate calculations and successful technological solutions, to the equipment manufacturer for the quality of execution, to the teams of installers and their managers for the efficiency and culture of assembling the evaporation station, and a big thank you to the investor for his trust.
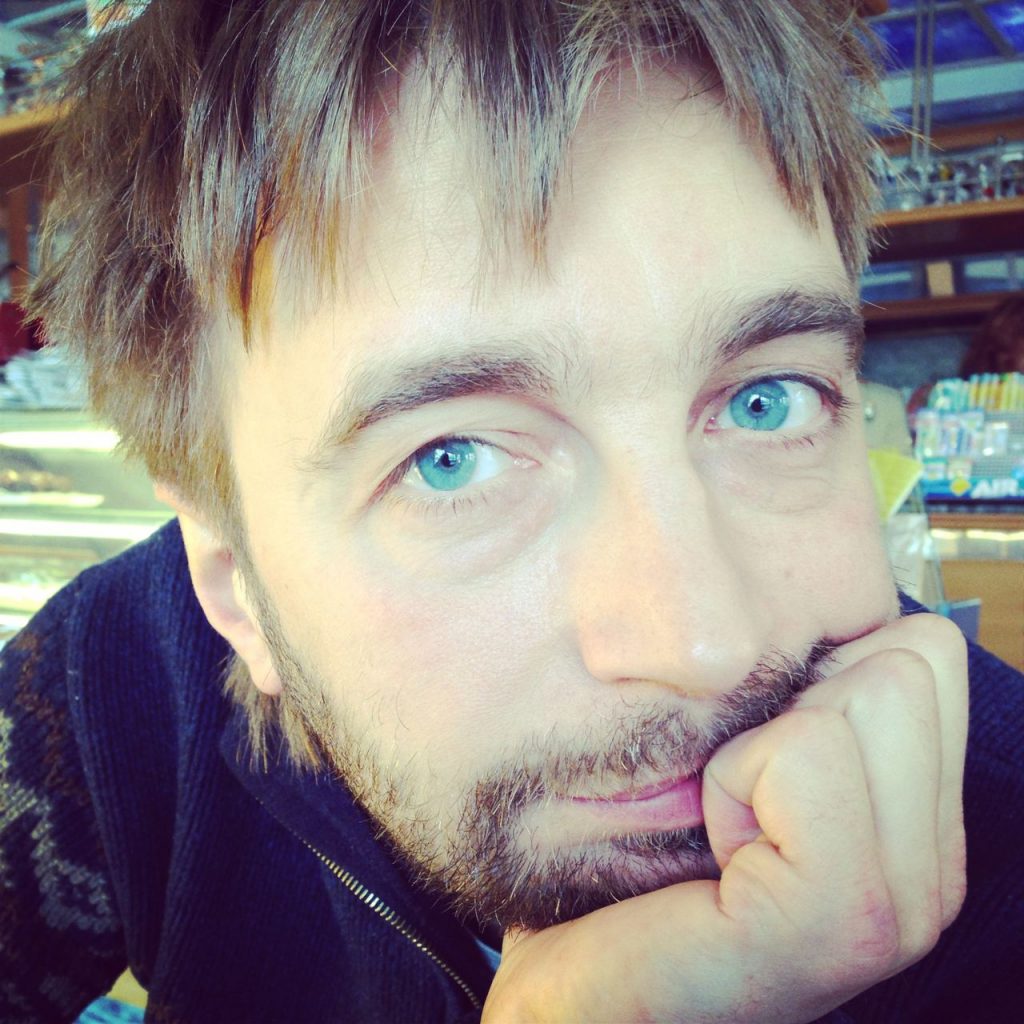