We conducted a pre-project study of future production, issued a hardware and technological diagram and developed specifications and requirements for equipment.
The next important stage in the creation of alcohol production is the production of equipment.
At Agrotechnology, we are responsible for the final result, so we entrust the production of equipment only to reliable partners. The products must strictly conform to the designed models and specifications.Since 2010, we have been placing production of equipment for alcohol and bioethanol at “Vinnitsa Experimental Plant”. This company operates according to our standards of culture and production quality.
HOW THE PRODUCTION PROCESS TAKES PLACE AT “VINNITSA EXPERIMENTAL PLANT”
When we already know what equipment is needed and have developed its sketches, we give them to the factory design office. There, the plant’s engineers create a detailed drawing of the product, select materials that correspond to operating modes and loads
Materials:
food-grade stainless steel of various brands, resistant to aggressive environments, is used for most types of alcohol equipment;
copper – if high organoleptic quality indicators of alcohol are required. Dephlegmators, rectification columns or their elements: valves, plates are collected from copper.
After agreement and approval of the technical task for the product, the drawings are sent to the workshops for production.
Modern digital equipment is used for production: horizontal boring machine, laser cutting. Turkish rollers, guillotines, 200-ton presses are also used. Machine operators, welders, fitters, millers, plant technologists do a good job of performing our tasks.
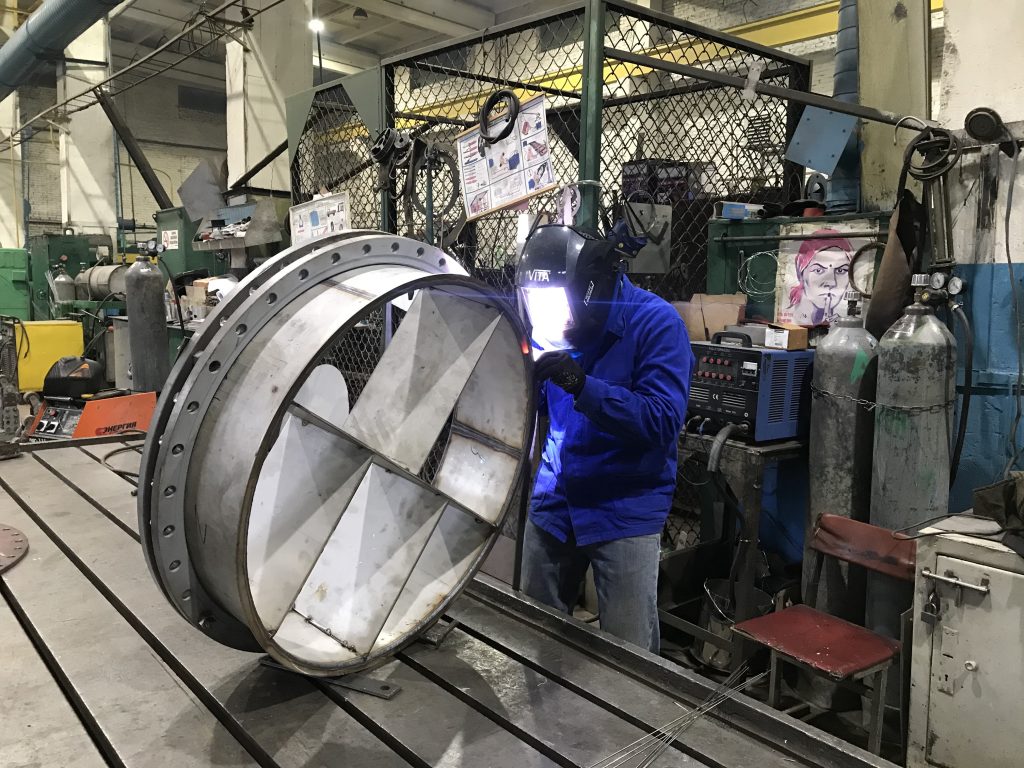
For example, you need to make an alcohol column. To do this, the technologist cuts the metal, cuts the metal on a guillotine, welds the cards, twists the core on the rollers (the rollers are good, with a bend), fasten the segments from the inside – a flange for the plates, and put on the flanges.
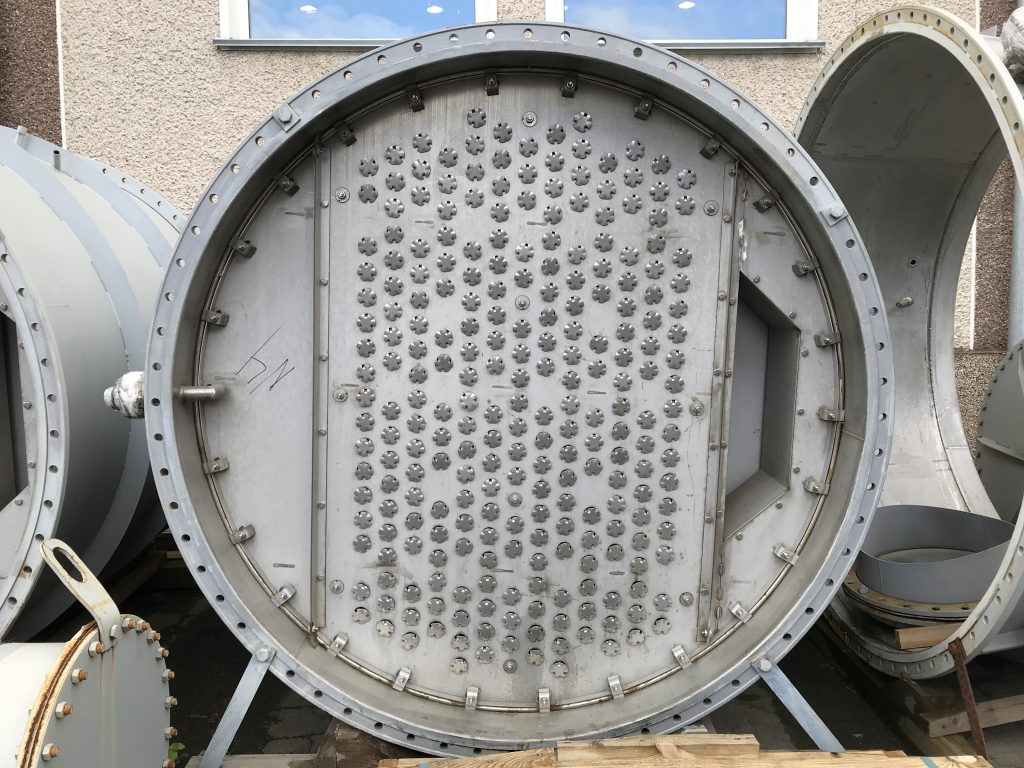
Before the start of the assembly, the places for the pipes are marked, the specialists of the technical control department make control measurements and if everything is OK, they give permission to install the plates. An intermediate structural element in the form of a frame, which is called “tsarga” is independent. In the case of the slightest mistake, tsarga is returned for revision. The product will not leave the factory if it does not meet the approved design documentation.
Plates are cut out with a laser, caps for them or other contact devices of the required shape are made on presses.
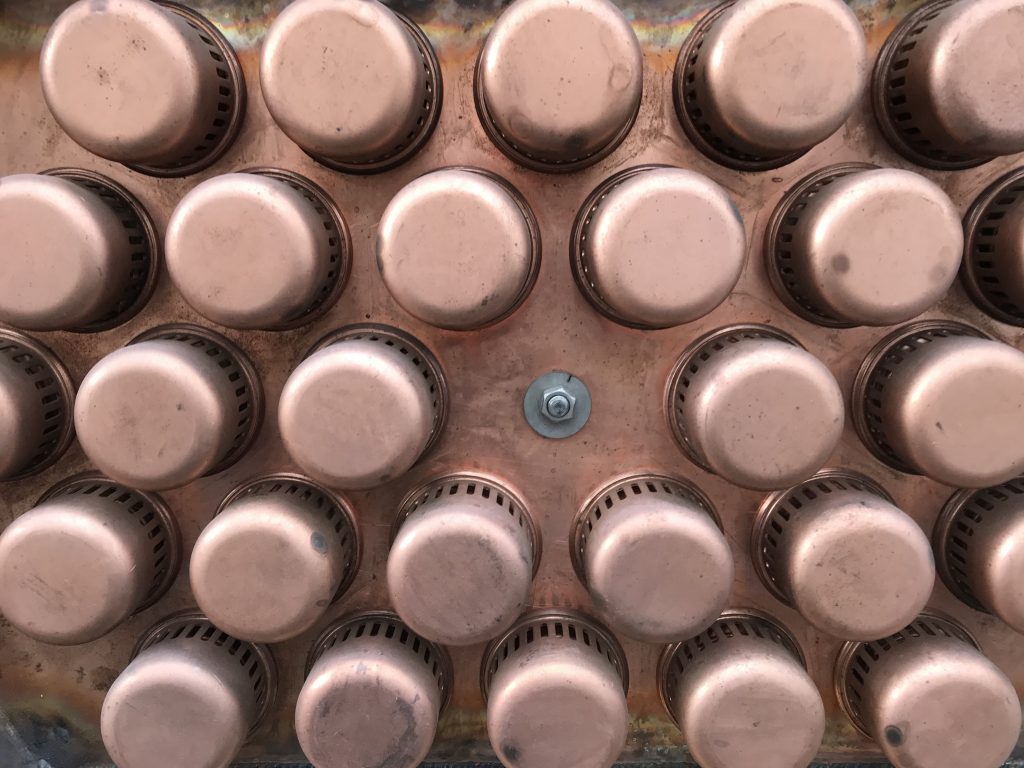
When the plates are installed, the overflow bars and glasses are mounted, the quality control checks the welds and soldering, sealing and tolerances.
Spherical column bottoms with a diameter of up to 3.5 meters are rolled out on special machines.
Finally, all the pipes are welded and the ends are painted in the color of your choice.
The largest rectification columns manufactured by the plant are 30 meters high and 2.4 meters in diameter.
The most difficult heat exchange equipment manufactured by the factory are falling-film evaporators (for an evaporation station with a capacity of 40 tons of evaporated moisture per hour for the processing of draff of the Haysynskyy distillery). Each has a heat exchange surface of 420 m2, a weight of 12 tons, a length of 13 meters, a diameter of 1.6 meters.
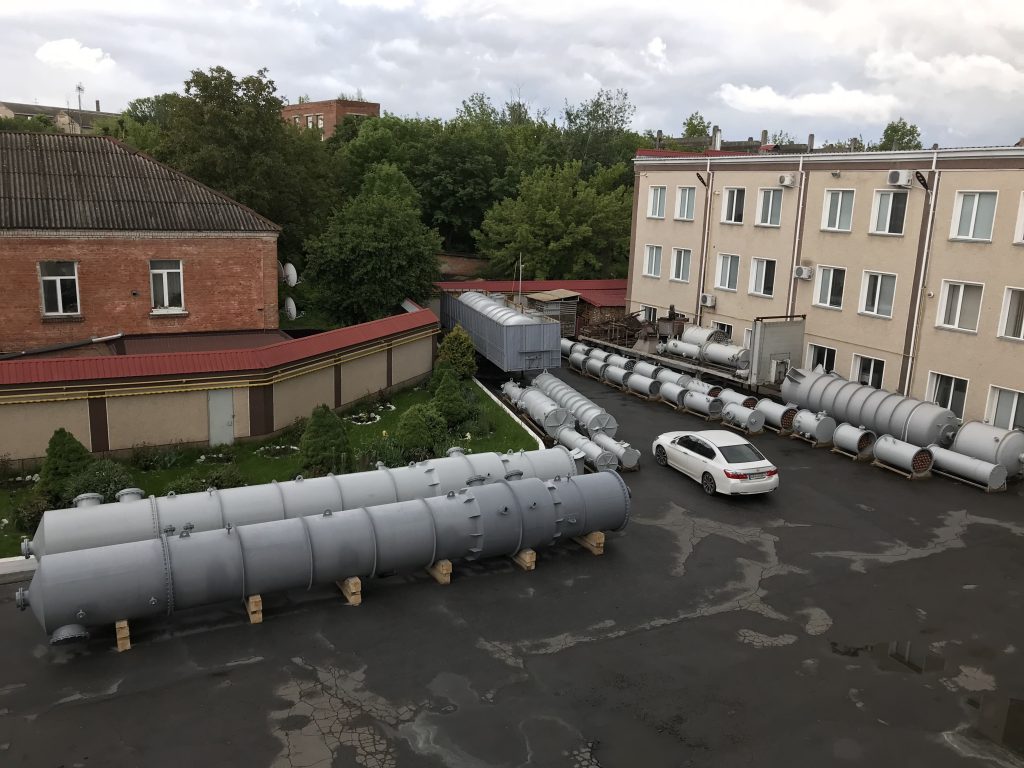
With the beginning of the privatization of the state distilleries of Ukraine, there was a need to replace the old energy-consuming equipment. The plant began production of complete steam rectification devices with multi-pressure, “Multi-steam” technology. Such devices consume 2.0…2.4 kg of steam per liter of food grade ethanol. Apparatus schemes and equipment design developed by “Agrotechnology” allow to produce products of the highest quality – the so-called “zero alcohol” or “neutral spirit”.
The equipment is ready. It is carefully packed, installed on the log for safe transportation. They load it into the vehicle, and here it is, ready for installation.Vinnitsa Experimental Plant equipment works at alcohol and cognac factories in Ukraine, Kazakhstan, Moldova, Belarus, Armenia, Azerbaijan and the Baltic countries.
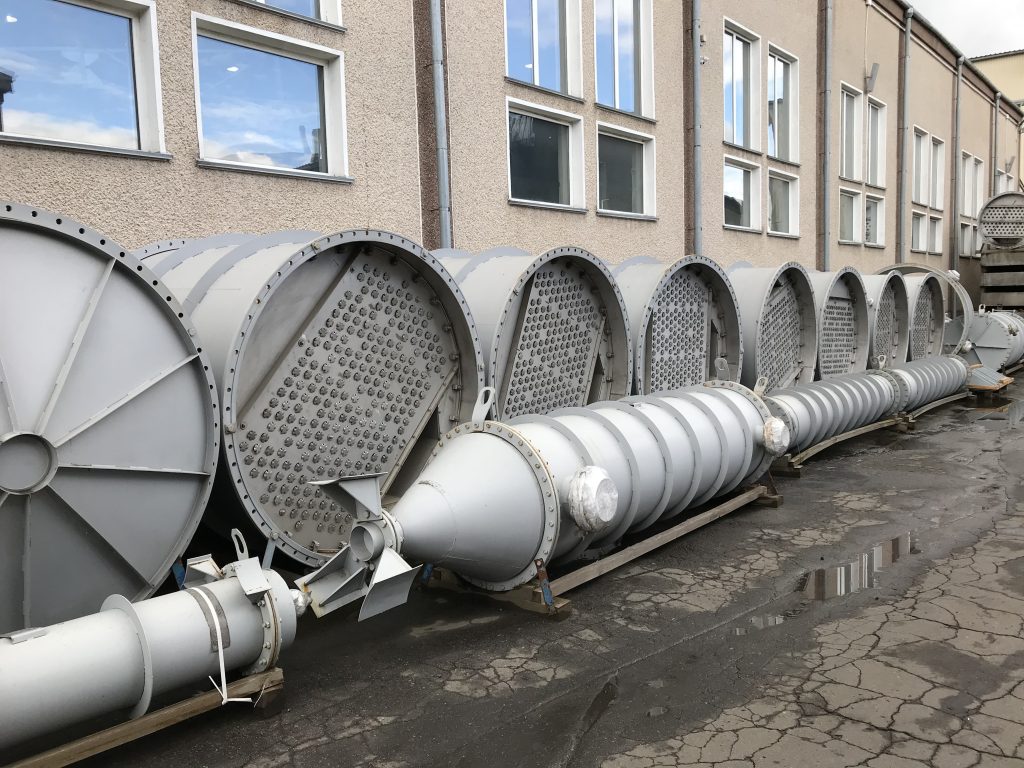