PROCESSING OF MOLASSES BARD
We reveal the energy potential of molasses bard – it is enough to provide the entire production with technological steam.
Our engineers create installations for thickening molasses bard and reducing its volume by 5-7 times, up to 55% of dry substances (DS).
1 ton of thickened vinasse replaces 200 m3 of gas or emits 3500 Mkal during combustion.
Bard with 55% DS is used as fertilizer and fuel.
We can get the energy of native bard, producing biogas from it: the output from 1 m3 of bard is 30 m3 of natural gas (methane) for the factory boiler room.
Download presentation [PDF]
Disposal of grain bard
We can build a grain bard processing line to DDGS or produce DDG and biogas.
PROCESSING OF GRAIN DRAFF
During the production of bioethanol by dry grinding, about one third of the dry matter of the grain turns into vinasse. The dry substance of the bard is polydisperse – from large settling particles to colloidal and soluble ones. When the bard is separated in the gravitational field (settling or centrifugation), a precipitate and clarified bard are formed.
By combined or separate dehydration of the sediment and clarified vinasse, four feed products can be obtained:
- Dried precipitate (DDG – Distillers Dried Grains).
- DDS – Distillers Dried Solutions.
- DDGS – Distillers Dried Grains with Solubles.
Condensed clarified vinasse with dry substances content from 30 to 40% (CDS – Condensed Distillers Solutions).
Abroad, bioethanol plants receive all of these types of products in accordance with local demand. However, most often grain bard is processed into DDGS as the most complete, transportable feed product of long-term storage.
The first stage of bard processing technology is its decantation – separation into a precipitate (wet cake) and a clarified bard (thin stillage).
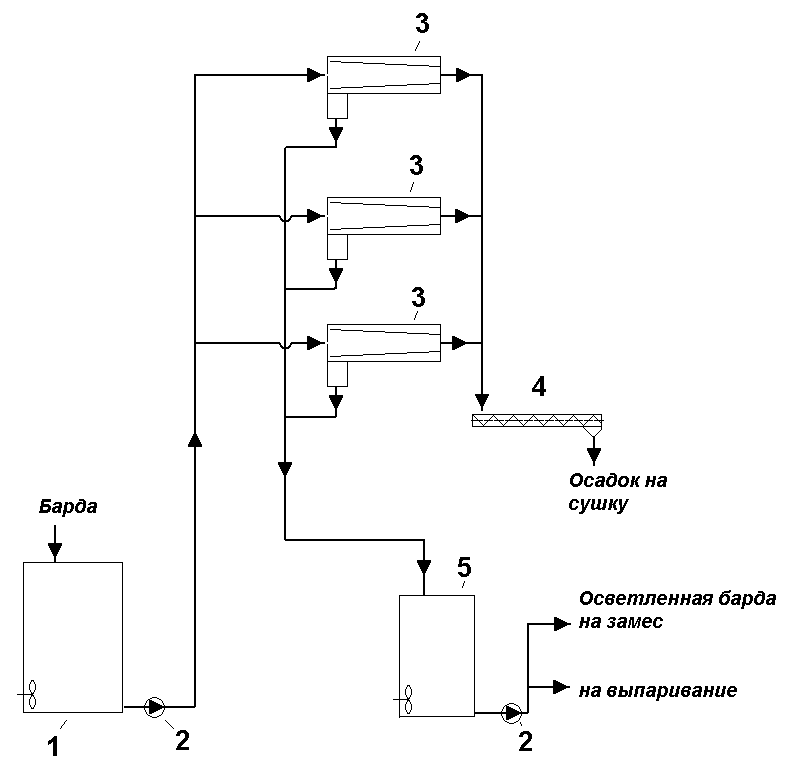
Usually, decantation is carried out in sedimentary horizontal screw centrifuges of continuous action 3. They can obtain a precipitate of about 70% humidity. Bard sludge is sometimes used raw as feed on nearby livestock farms under the name DWG – Distillers Wet Grains.
Usually 2-4 centrifuges are installed, one of which is in reserve. Bard from assembly 1 is transferred by pump to centrifuges 3. The temperature of the bard is within 50… 95 ° C, depending on the scheme of using its heat for heating other technological intermediates, for example, the brew. The clarified bard flows down to the collector 5, and the precipitate is transferred by the conveyor 4 for drying.
The balance of products at the stage of decantation of bard is as follows (Fig. 2). The balance of the existing plant with a capacity of 320 m3 of bioethanol per day, raw materials – corn. The bard of bioethanol plants has an increased content of dry substances (12… 13%) compared to food alcohol plants (7… 9%). This is due to the return of part of the bard for kneading, which is rarely used in food alcohol factories due to fears of deteriorating its quality.
The lighted bard partially (about 30%) returns to the preparation of the batch. The rest of it is sent for thickening by evaporation of water in a vacuum evaporator.
Thickening of the bard is a rather energy-intensive process. Therefore, for its implementation evaporative installations are used, which maximize the full use of thermal energy. This approach requires significant costs for heat exchange equipment, but allows you to reduce current energy costs and avoid environmental pollution by production waste. The cost of bard processing equipment exceeds 35% of the cost of all technological equipment of the bioethanol plant.
Two main thermal schemes are used to evaporate the clarified bard. According to one of them, the operation of the evaporator is provided by the heat of the steam-air mixture from the bard dryer. By other – the heat of fresh boiler steam, and the secondary steam from the evaporator is used to heat the columns in the bragorectification compartment.
Here ia the scheme of evaporation of the bard due to the secondary heat of the dryer.

The designs of the dryers will be discussed below, but common to them is the output stream of the steam-gas mixture having sufficient thermal potential for evaporation of the bard. As a rule, these are dryers heated by burning natural gas or liquid fuel.
In Fig. 3, the numbers 1, 2 and 3 indicate the first, second and third evaporators (housing) of the installation. Design of evaporators – with falling film of evaporating liquid and with forced circulation. The first case is heated by a steam-gas mixture from a dryer with a temperature of 80… 95 ° C. The water vapor is condensed in the first housing and the gases are discharged to the heat exchanger 4, cooled by the water and discharged into the atmosphere. In the third case, a solution is evaporated, already partially condensed in the first and second cases. After decantation, the illuminated bard is fed to the first housing of the installation, which is heated by the secondary steam of the third housing. The second housing is heated by the secondary steam of the first, and the secondary steam of the second housing enters the condenser 5, which is cooled by water and is under vacuum. The condensates of the secondary steam from the first, second housings and the condenser 5 are called acid condensates and are used to prepare kneading. Condensates of the third housing and condenser 4 formed from the steam-gas mixture are discharged separately and sent for purification.
A characteristic feature of the installation is the low temperature pressures between the heating steam and the liquid due to the small total temperature difference between the heating steam in the housing 1 and the steam in the condenser 5. On the one hand, this requires large heat exchange surfaces of the apparatuses and forced circulation. On the other hand, it reduces the thermal decomposition of the product and pollution of the heat exchange surfaces.
Such evaporators are not associated by heat flows with areas of bragorectification and dehydration of ethanol. Together with the drying unit, they form a separate technological unit, which can be designed and built not immediately, but later.
Another bard thickening scheme is integrated by heat flows from bragorectifications and bioethanol dehydration, other process areas (Fig. 4).
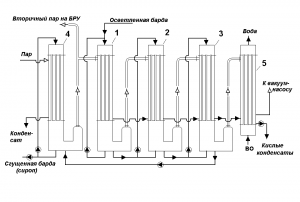
Heating of the fourth housing of the evaporator is carried out by boiler steam. Part of the secondary steam of the fourth building, and sometimes the second and third are used in other technological areas – for heating columns operating under vacuum, heating intermediates. Such evaporators are used when steam dryers for bard are installed, that their exhaust heat is impractical to use.
The technology of thickening clarified vinasse and joint drying of the resulting syrup with sediment is easiest to imagine in the form of a scheme of material balance
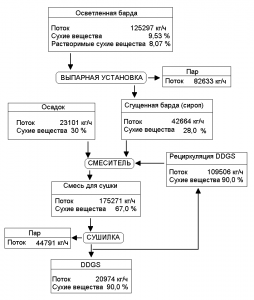
To dry the mixture of thickened vinasse and sediment, various types of dryers are used: drum, ring, dryers with indirect heating of the dried material, vacuum dryers.
The drying agent used is natural gas combustion products mixed with air or (more often) air heated in heaters. In the second case, product is more consistent with veterinary requirements.
To obtain a high quality feed product, it is necessary to avoid heating it above 65… 70 ° C. Otherwise, due to the Maillard reaction, the amount of indigestible protein increases in it. The most gentle drying mode is provided by drum and ring dryers, to which hot air is supplied. The second place in the quality of the dried product is occupied by vacuum dryers with indirect heating of the dried product with low potential steam. However, despite the high energy efficiency, they are metal-intensive and difficult to operate.
Atmospheric pressure dryers with indirect heating allow a higher heating temperature of the dried product and a decrease in its quality.
Sometimes a two-stage process is used to achieve high quality: at the first stage, the material is dried with hot air heated by combustion products, the steam-air mixture of the first stage is used to evaporate the clarified vinasse, and at the second stage, drying is carried out with warm air after the steam calorifer.
The scheme of drying the bar using a drum dryer is shown in Fig. 6.
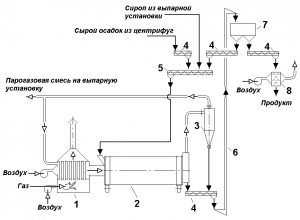
The combustion products of natural gas heat the air in the calorifer 1. Hot air enters the drum of the dryer 2, where a mixture of raw sludge, syrup (condensed clarified vinasse) and part of the dried product is fed from the mixer 5.
The dried product from the norium dryer 6 is lifted into the intermediate hopper 7, where part of the product is returned to the mixer 5 and the rest is passed through the cooler 8.
The steam-gas mixture leaving the dryer passes through the cyclone 3, where it is released from the dusty particles of the product, and is sent to the evaporator for heating the first housing.
After drying, the product is air-cooled and sent to the composition. Bulk weight of the product is 0.45… 0.55 t/m3, angle of natural slope ~ 30°.
Sometimes, the dried product is granulated in special continuously operating press granulators. Granules usually have diameter of 8-10 mm, length of 10-20 mm, humidity of 10-12%, bulk weight of 0.60-0.65 t/m3.
The dried vinasse is stored mainly in floor storage compositions.
The resulting product contains insoluble and soluble components of the vinasse and is called DDGS. It is a concentrate of all components of the grain (except starch, which has turned into ethanol and carbon dioxide in the technological process). This feed product is new for the CIS countries, although in the USA and Canada it has been produced and consumed in animal husbandry for more than 15 years. Recently, its production has exceeded 20 million tons per year.
This product has high hopes for the development of local livestock, because in the areas where bioethanol plants are located, cheap high-quality concentrated feed appears. The approximate composition and some feed properties of DDGS are given in Table 1.
Table 1
COMPOSITION AND SOME PRINCIPAL PROPERTIES OF DDGS
№ | Characterists |
Сompound |
1 | Dry matter content (DM) % wt. | > 90 |
2 | Total fat, g/kg of DM | 70 |
3 | Total protein, g/kg of DM | 340 |
4 | Nitrogen-free extractive substances, g/kg of DM | 475 |
5 | Ash, g/kg of DM | 46 |
6 | Total fiber (cellulose, etc.), g/kg of DM | 66 |
7 | Calcium, g/kg of DM | 2,3 |
8 | Phosphorus, g/kg of DM | 9,6 |
9 | Magnesium, g/kg of DM | 2,8 |
10 | Potassium, g/kg of DM | 10,9 |
11 | Sodium, g/kg of DM | 0,6 |
Amino acids: | ||
12 | Cystine, g/kg of DM | 7,3 |
13 | Methionine, g/kg of DM | 5,2 |
14 | Threonine, g/kg of DM | 10,7 |
15 | Lysine, g/kg of DM | 9,6 |
16 | Over-zealous protein (for ruminants), g/kg of DM | 295 |
17 | High over-treatment protein (for pigs), g/kg of DM | 208 |
18 | Metabolic energy (for ruminants), MJ/kg of DM | 13,7 |
19 | Метаболическая энергия (для свиней), МДж/кг СВ | 11,1 |
The quality of this product largely depends on the technology used in bioethanol plants. According to the results of our research, the feed value of the product is most influenced by the temperatures at which the corn is dried before loading it into the elevator, the technology of wort preparation for ethanol fermentation (fermentation), the bragging scheme, the thermal modes of evaporation of the bard, drying of the sediment and condensed bard. At all stages of the process, it is necessary to avoid temperatures above 80 ° C, and during drying – above 65… 70 ° C.
The effect of excessive heating of the process products most accurately reflects the content of residual nitrogen after acid washing of ADIN (Acid Detergent Insoluble Nitrogen), or the amount of nitrogen in the fraction washed with a solution of fibrous acid – ADF (Acid Detergent Fiber).
ADIN in countries with developed production of DDGS is one of the main indicators of the quality of this product.
An additional, but inaccurate indicator of feed quality is the color of the product. Corn DDGS of high feed conditions should have a honey-golden color. The transition to dark coffee color indicates overheating of the product in the process and a potentially high level of ADIN.
In the global market, the cost of a ton of so-called “gold” DDGS (ADIN content up to 6%) is on average 20… 25 US dollars higher than usual. It is a full-fledged alternative to soy meal in feed.
In the United States and Canada, DDGS takes up about 20% of the dry matter in the diet of dairy cows. Balancing rations is carried out not only by the protein content (maximum 18%), but also by the content of phosphorus, which is a limiting factor. Its content should exceed 0.4% of dry substances of the diet, and DDGS phosphorus content is from 0.8 to 1.0%. Other factors that should be taken into account when using this product for feed purposes are the prevention of lysine deficiency and excess fat (no more than 6%) in the diet. Taking into account all these factors, the content of DDGS in the diets of dairy cows can reach 30%. Approximately, the following maximum DDGS content in the dry matter feed balance, %:
- Lactating cows 20
- Cattle for fattening 40
- Fattening pigs 20
- Birds 10
Taking into account the requirements for the quality of this feed product, which will be produced at domestic plants in significant quantities (according to cautious estimates about 800 thousand tons in 2012), the Institute of Food Biotechnology and Genomics of the NAS of Ukraine (IFBG) has developed recommendations for the technological design of enterprises. They relate to the technological areas of dilution and icing of wort, bragging, evaporation and drying of the feed product and are accepted for implementation in the factories under construction.
Development of technological schemes, selection or development and manufacture of equipment for these areas is carried out on the recommendations of Agrotechnologie.
Comparative feed value of bard processing products is given in Table 2.
Table 2
COMPARATIVE FEED VALUE OF DRAFF PROCESSING PRODUCTS
Characteristic | DDG | CDS | DDGS |
Dry matter (DM), % | 94 | 30 | 90 |
Total protein, % | 23 | 30 | 25 |
A protein that is not digested by ruminants, % of total protein | 47…63 | 47…63 | 47…63 |
Fat, % of SV | 10 | 9 | 10 |
АDIN (ADF), % of DM | 17 | 7 | 18 |
NDF*, % of DM | 43 | 23 | 44 |
* Neutral Detergent Fiber (amount of nitrogen in the fibrous fraction washed with neutral water).
It can be said that bioethanol plants produce two equivalent types of products – biofuel and concentrated animal feed.